Jakie są etapy prac antykorozyjnych?
Proces zabezpieczania konstrukcji przed korozją można podzielić na trzy kluczowe etapy:
- Przygotowanie powierzchni, obejmujące mycie i czyszczenie.
- Aplikację powłok, do której zalicza się metalizację i malowanie.
- Kontrolę procesu za pomocą specjalistycznych urządzeń kontrolno-pomiarowych.
Czystość powierzchni przed malowaniem znacząco wpływa na trwałość i jakość powłok ochronnych. Odpowiednie przygotowanie powierzchni pozwala usunąć produkty korozji oraz wszelkie zanieczyszczenia, a także nadać strukturze odpowiednią chropowatość, co poprawia przyczepność powłok antykorozyjnych.
Wybór metody przygotowania powierzchni
Przed rozpoczęciem prac należy przeanalizować:
- rodzaj i ilość zanieczyszczeń,
- materiał podłoża,
- wielkość i kształt powierzchni,
- agresywność środowiska,
- rodzaj systemu powłokowego,
- przewidywaną trwałość pokrycia,
- wymagania dotyczące czystości powierzchni,
- warunki użytkowania i przeznaczenie obiektu.
Mycie konstrukcji przed czyszczeniem
Pierwszym krokiem w czyszczeniu konstrukcji jest mycie wodą, które pozwala skutecznie usunąć błoto, sól, olej i smary. Najczęściej stosuje się urządzenia wysokociśnieniowe generujące ciśnienie wody około 20 MPa.
W ostatnich latach coraz częściej stosuje się myjki o ciśnieniu nawet do 50 MPa, co umożliwia usunięcie zanieczyszczeń z trudno dostępnych miejsc, takich jak szczeliny czy spoiny. Do czyszczenia konstrukcji mostowych producenci oferują pompy wysokociśnieniowe na własnych podwoziach, napędzane silnikami spalinowymi, co zapewnia ich mobilność i wydajność.
Jeśli na powierzchni występują trudne do usunięcia substancje oleiste, stosuje się urządzenia z podgrzewaczem wody oraz specjalne detergenty, które skutecznie eliminują zabrudzenia maziste.
Czyszczenie powierzchni
Po myciu następuje proces właściwego czyszczenia, który pozwala uzyskać wymaganą czystość pod aplikację powłok ochronnych. Najczęściej stosowane metody to:
- Czyszczenie strumieniowo-ścierne – realizowane przy użyciu piaskarek i różnych ścierniw, takich jak śrut, elektrokorund czy szlaka pomiedziowa.
- Czyszczenie wodą pod wysokim ciśnieniem – wykonywane z użyciem urządzeń hydrodynamicznych.
Piaskowanie jest jedną z najbardziej efektywnych metod przygotowania powierzchni. Wykorzystuje się oczyszczarki pneumatyczne, które działają na bazie sprężonego powietrza o ciśnieniu od 6 do 12 barów. W zależności od specyfiki projektu stosuje się różne rodzaje ścierniw – od piasku, przez kulki szklane, aż po śrut staliwny.
Piaskarki do piaskowania na sucho wyposażone są w precyzyjne zawory dozujące ścierniwo, co pozwala na kontrolę intensywności obróbki. Oczyszczarki do śrutu posiadają dodatkowe zabezpieczenia zaworów, co zwiększa ich żywotność i efektywność pracy.
Dobrze dobrana metoda czyszczenia zapewnia maksymalną trwałość i skuteczność powłok antykorozyjnych, co przekłada się na dłuższą ochronę konstrukcji przed szkodliwym działaniem czynników zewnętrznych.ę konstrukcji przed szkodliwym działaniem czynników zewnętrznych.
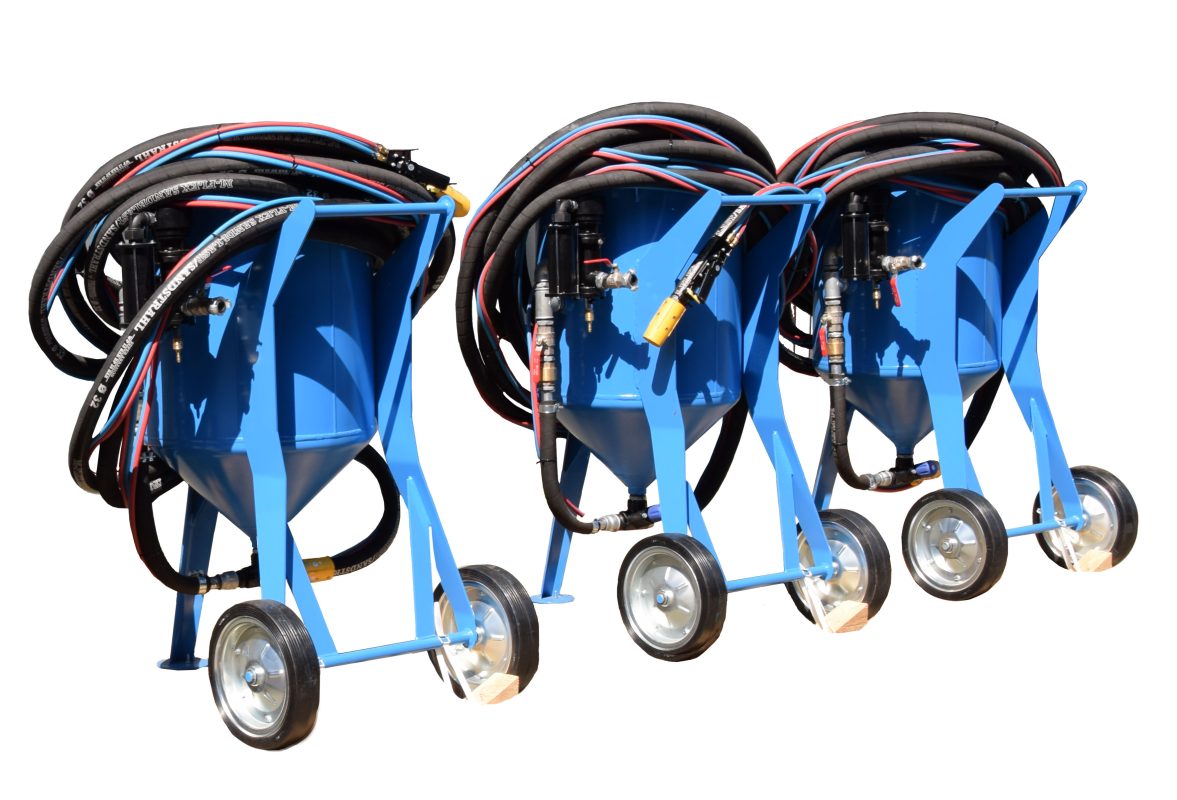
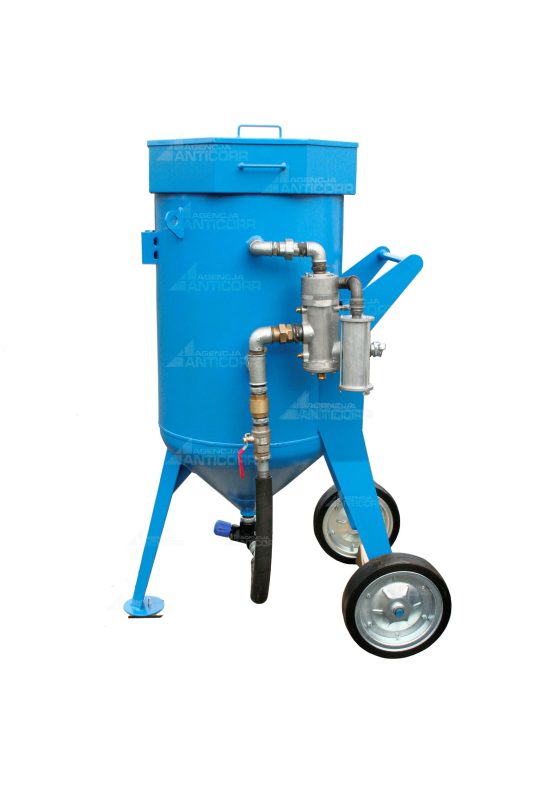
Dostępne systemy pozwalające na piaskowanie powierzchni na mokro podłączane są bezpośrednio do dyszy. Woda w zależności od modelu głowicy musi być podana pod ciśnieniem z pompy lub bezpośrednio z sieci jeżeli ciśnienie mieści się w zakresie od 2-6 bar.
Metalizacja
Metalizacja – Proces, Zastosowanie i Korzyści dla Przemysłu
Metalizacja to zaawansowana technologia, która pozwala na nadanie stalowym powierzchniom wyjątkowych właściwości ochronnych i estetycznych. Dzięki metalizacji uzyskujemy trwałe powłoki, które zapewniają skuteczną ochronę przed korozją, a także zwiększają odporność na ścieranie i regenerują zużyte elementy maszyn. Dodatkowo, metalizacja może podkreślać walory estetyczne powierzchni, co jest istotne w wielu branżach przemysłowych.
Jak działa proces metalizacji?
Proces metalizacji polega na podgrzaniu metalu do temperatury topnienia, a następnie naniesieniu go na powierzchnię za pomocą strumienia gazu (najczęściej sprężonego powietrza). W zależności od źródła ciepła, wyróżniamy dwa główne typy metalizacji:
- Metalizacja gazowa (płomieniowa) – metal topnieje w płomieniu gazu (propan lub acetylen).
- Metalizacja łukowa (elektryczna) – proces topnienia metalu przy użyciu łuku elektrycznego.
Do metalizacji łukowej wykorzystywane są zestawy z jednostkami zasilającymi, pistoletami do metalizacji, podajnikami drutu i odpowiednimi kablami. Wybór zestawu zależy od wymaganej mocy, dostępne są modele o natężeniu prądu 300A, 400A lub 600A.
Malowanie ochronne – Zabezpieczenie przed korozją
Malowanie ochronne ma kluczowe znaczenie w zapobieganiu korozji atmosferycznej. Celem jest nie tylko zabezpieczenie powierzchni przed rdzą, ale także nadanie jej odpowiedniego wyglądu i tekstury. Dzięki technice natryskowej, farba nakładana jest równomiernie i szybko, co zapewnia lepsze efekty estetyczne i trwałość powłok.
Wraz z rozwojem technologii, urządzenia do malowania ochronnego koncentrują się na zmniejszeniu odpadów farb, rozpuszczalników i opakowań. Nowoczesne agregaty malarskie pozwalają na równomierne nanoszenie różnych preparatów, takich jak farby, emalie, lakiery czy tynki, przy minimalnym marnotrawstwie materiału.
Kontrola jakości – Gwarancja trwałości i wydajności
Każdy etap metalizacji i malowania wymaga szczegółowej kontroli jakości, aby zapewnić wysoką trwałość powłok ochronnych. W tym celu wykorzystywane są specjalistyczne urządzenia pomiarowe, które pozwalają na dokładną ocenę takich parametrów jak:
- grubość warstwy powłoki,
- twardość,
- przyczepność,
- szczelność,
- czystość podłoża.
Kontrola jakości zapobiega potencjalnym błędom, które mogłyby wpłynąć na trwałość powłok ochronnych i estetykę powierzchni.
Pomiar grubości powłok
Grubość powłok to jeden z najważniejszych parametrów kontrolowanych podczas metalizacji i malowania. W zależności od rodzaju powłok, stosowane są różne metody pomiarowe:
- Pomiar grubości powłok mokrych – przyrząd mierniczy jest przykładany do mokrej powierzchni, a wynik odczytywany jest na podstawie kontaktu przyrządu z warstwą powłoki.
- Pomiar grubości powłok suchych – do pomiaru wykorzystuje się mierniki mechaniczne (np. magnesy) oraz elektroniczne, które bazują na indukcji magnetycznej lub prądach wirowych. Mierniki elektroniczne oferują dodatkową funkcjonalność, umożliwiając przechowywanie wyników i ich obróbkę.
Pomiar przyczepności powłok
Przyczepność powłok, czyli zdolność ich przywierania do podłoża, jest jednym z kluczowych parametrów jakościowych. Pomiar przyczepności może być wykonywany różnymi metodami:
- Metoda odrywowa – ocenia siłę, jaką należy zastosować do oderwania powłoki od podłoża.
- Metoda nacięć – ocenia przyczepność poprzez wykonanie nacięć na powierzchni powłoki i ocenę wyników po przeszczotkowaniu i próbce odrywania taśmą klejącą.
Pomiar warunków klimatycznych
Warunki klimatyczne mają istotny wpływ na trwałość powłok ochronnych. Właściwa temperatura, wilgotność i punkt rosy są kluczowe dla uzyskania najlepszych efektów podczas metalizacji i malowania. Dlatego pomiar tych parametrów odbywa się na każdym etapie procesu.
Pomiar chropowatości powierzchni
Chropowatość powierzchni wpływa na przyczepność powłok oraz ich trwałość. Pomiar chropowatości przeprowadzany jest za pomocą specjalistycznych mierników chropowatości, które pozwalają na ocenę różnych parametrów powierzchni. Mierniki elektroniczne umożliwiają dokładne określenie chropowatości, a także zapisywanie wyników i ich analizę.
Zalety stosowania nowoczesnych technologii
Inwestowanie w nowoczesne urządzenia do metalizacji, malowania i kontroli jakości przynosi długofalowe korzyści. Dzięki takim rozwiązaniom możliwe jest:
- zwiększenie efektywności procesów,
- redukcja strat materiałów,
- szybsza realizacja zleceń,
- poprawa jakości produktów,
- spełnianie wymagań ochrony środowiska.
Dobrej jakości urządzenia pozwalają na bezpieczną i efektywną pracę, jednocześnie minimalizując wpływ na środowisko naturalne. Dzięki temu przedsiębiorstwa mogą poprawić swoją konkurencyjność i generować oszczędności.