Śrutownia może być wyposażona w pełny mechaniczny system obiegu ścierniwa, co pozwali na skrócenie przerw podczas oczyszczania oraz na zmniejszenie potrzebnej ilości ścierniwa w obiegu. Opadające na powierzchnię podłogi ścierniwo jest zgarniane mechanicznie do brzegu komory, skąd jest pobierane przez podnośnik kubełkowy i podawane do bębnowego separatora ścierniwa. Po oczyszczeniu w separatorze bębnowym ścierniwo spada do zbiornika zasobowym. Pod zbiornikiem jest zainstalowany jeden dozownik ścierniwa. Zasypywanie dozownika ścierniwem odbywa się automatycznie w czasie przerw w pracy. Rozpoczęcie i zakończenie procesu oczyszczania sterowane jest przez operatora poprzez przyciśnięcie lub popuszczenie przełącznika ręcznego montowanego na wężu śrutowniczym za dyszą.
Śrutownia jest wyposażona w dwukomorowy moduł do odciągania i oczyszczania brudnego powietrza. Powietrze po oczyszczeniu jest zawracane do komory.
Przykładowa budowa komory śrutowniczej
Konstrukcja komory śrutowniczej
Komora jest zbudowana ze szkieletu stalowego obudowanego płytą warstwową o grubości 60mm. Zostanie posadowiona na stalowej ramie, dzięki czemu nie będzie trzeba wykonywać prac fundamentowych pod śrutownie.
Drzwi główne i serwisowe
Komora jest wyposażona w jedną bramę rolowaną oraz w jedne drzwi serwisowe.
Osłona przed oddziaływaniem ścierniwa
Ściany, sufit, brama oraz drzwi bezpieczeństwa komory, są zabezpieczone od wewnątrz osłonami gumowymi o grubości 3mm. Zostały one zamontowane w sposób gwarantujący swobodny opad ścierniwa na podłogę zgarniającą.
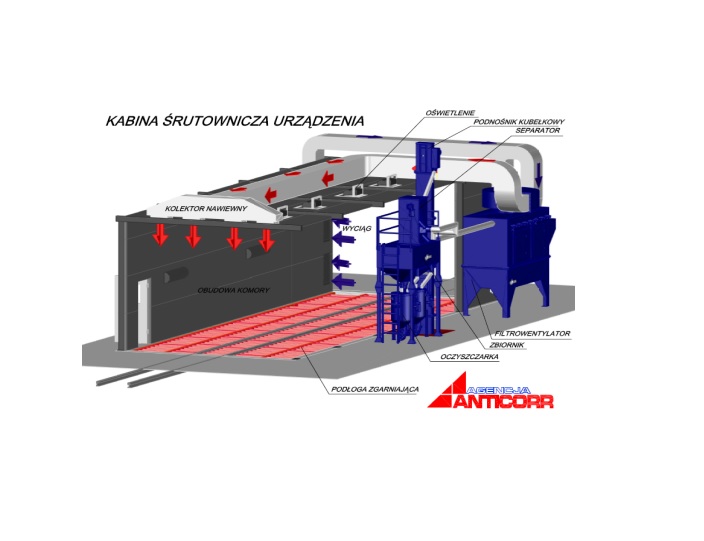
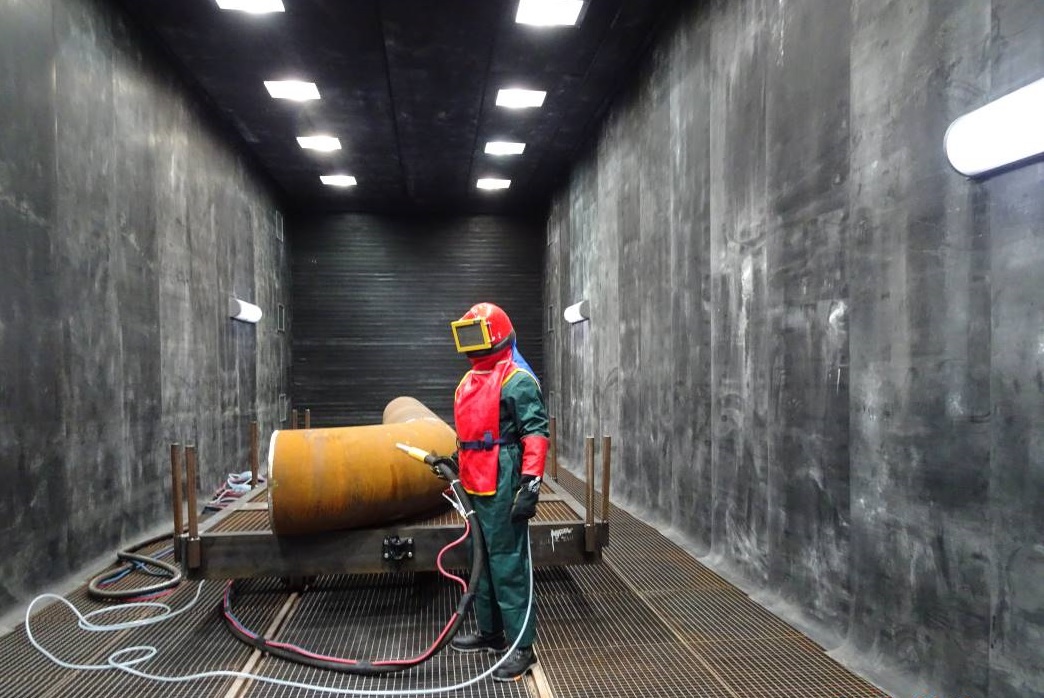
Oświetlenie w komorze
Komora do obróbki strumieniowo-ściernej jest oświetlana przez szereg lamp LED usytuowanych na komorze. W suficie komory zainstalowano specjalne kasetony ze szkła, ponad którymi są umocowane lampy. Dostęp do lamp jest możliwy od góry komory do obróbki strumieniowo-ściernej i, bez konieczności demontowania kasetonów. Zamontowane zostało także oświetlenie bezpieczeństwa.
System wentylacyjno-odpylający
Komora jest wyposażona w system wentylacji składający się z wentylatora, dwukomorowego modułu filtracyjnego i kanałów. Oferuje się system wentylacji z zawracaniem powietrza po przefiltrowaniu. Zapylone powietrze jest odciągane, oczyszczane w wysokowydajnym dwustopniowym module filtracyjnym. Najpierw jest oczyszczane w filtrze komorowym, a następnie na suchych filtrach poliestrowych.
Oczyszczone powietrze jest zawracane w ok 90% do komory. Zawracanie powietrza do śrutowni umożliwia zachowanie korzystnych warunków klimatycznych wewnątrz (temperatura i wilgotność). Oferuje się także wkłady filtracyjne wykonane z poliestru. Są one bardzo trwałe /ok. 5 lat do wymiany/. Zapewniają dokładne oczyszczenie powietrza. W przeciwieństwie do filtrów papierowych, są odporne na wodę i olej oraz przylepianie się cząstek stałych, przez co ich powierzchnia filtracyjna nie ulega znaczącemu zmniejszeniu podczas eksploatacji. W przypadku zabrudzenia wkłady poliestrowe można umyć, wysuszyć i dalej eksploatować. Niskie zapylenie oczyszczonego powietrza uzyskiwane na filtrach poliestrowych umożliwia wprowadzenie go z powrotem do śrutowni. Jedynie nadmiar powietrza jest wydalany na zewnątrz.
Do wyciągania powietrza z komory do obróbki strumieniowo-ściernej na obu bokach komory znajdą się dwa pionowe dyfuzory. Pobierane przez nie powietrze kanałami transportowane jest do modułu filtracyjnego. W suficie po stronie przeciwnej do wyciągów znajduje się wlot oczyszczonego powietrza. Do wyciągania powietrza z komory i jego odpylania ze skutecznością umożliwiającą wydalanie nadmiaru do atmosfery, zamontowano dwukomorowy moduł filtracyjny SUMF10/2, z dołączanym wentylatorem posiadający następujące parametry:
rodzaj wkładów filtracyjnych: | suche, poliestrowe, |
sposób oczyszczania: | rewersyjnie, sprężonym powietrzem, |
sposób regeneracji wkładów filtracyjnych: | mycie wodą pod ciśnieniem, |
zawartość pyłów w wydalanym powietrzu: | poniżej 4 mg/m3, |
trwałość wkładów filtracyjnych: | ok. 5 lat |
powierzchnia filtrów: | ok. 144m2, |
wydajność wentylatora: | 10.000m3/godzinę, |
moc silnika : | 11 kW . |
.
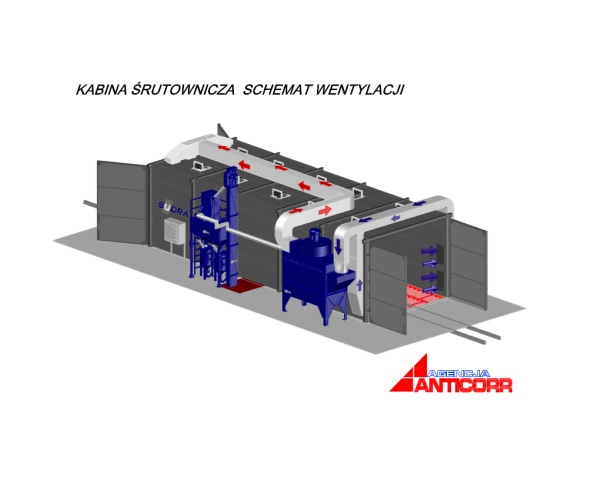
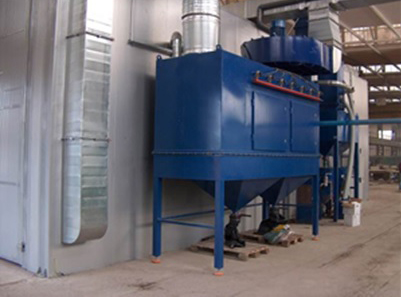
Podłogowy zgarniacz ścierniwa
Do zgarniania ścierniwa z podłogi w komorze zainstalowano zintegrowany system SUPZ5.3/E. Zgarnianie ścierniwa z podłogi odbywa się za pomocą ułożonych na podłodze modułowych korytarzy. Korytarz jest zbudowany z prowadnic bocznych wykonanych z profili zamkniętych oraz podwieszanej na rolkach ramy z umieszczonymi w regularnych odstępach zgrzebłami z listwą elastyczną. Zgarnianie ścierniwa odbywa się na zasadzie ruchu posuwisto zwrotnego wytwarzanego przez system motoreduktorów. W ruchu do przodu zgrzebła przesuwają się po powierzchni ścierniwa (bieg jałowy), natomiast w ruchu powrotnym zgrzebła opadają przesuwając ścierniwo (bieg pracy). Modułowe korytarze ułożone są na całej powierzchni komory śrutowniczej, tworząc zgarniacz podłogowy ścierniwa. Korytarze wzdłużne przesuwają opadające ścierniwo do miejsca w którym umieszczono korytarz poprzeczny umiejscowiony pod korytarzami wzdłużnymi.
Korytarz poprzeczny transportuje ścierniwo do boku komory, skąd ścierniwo jest pobierane przez podnośnik kubełkowy.
Podłoga pod zgarniakami wyłożona jest blachą stalową co uchroni betonową posadzkę przed oddziaływaniem ścierniwa i znacznie wydłuży żywotność zgarniaków.
W skład zgarniacza podłogowego SUPZ5.3/E wchodzi:
- 1 korytarz wzdłużny, umieszczony między torowiskiem, o szerokości 1300mm i długości 5m,
- 2 korytarze wzdłużne o szerokości 825mm i długości 5m,
- korytarz poprzeczny o szerokości 910 mm i długości 3m,
- wykładzina z blachy stalowej o grubości 3mm,
- kraty podestowe przeznaczone do ruchu pieszego.
*Podane wyżej wielkości są wymiarami sugerowanymi i oferent zastrzega sobie możliwość zmiany szerokości korytarzy po wykonaniu obliczeń oraz projektu podłogi zgarniającej.
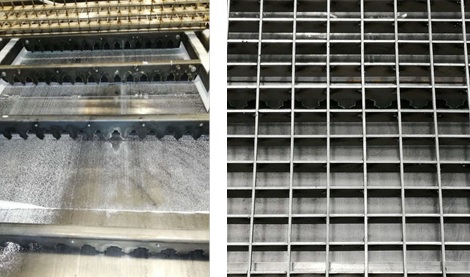
Pozostałe urządzenia do transportu, oczyszczania i dozowania ścierniwa
Śrutownia jest wyposażona w zintegrowany system do transportu, oczyszczania i dozowania ścierniwa składający się z podnośnika kubełkowego, separatora bębnowego, zbiornika zasobowego i dozownika śrutu.
Ścierniwo jest transportowane przez poprzeczny korytarz do boku śrutowni, skąd jest pobierane przez podnośnik kubełkowy i transportowane do separatora ścierniwa.
Podnośnik kubełkowy SUPK100/5 transportuje ścierniwo do separatora ścierniwa. Podnośnik jest wyposażony w napęd o mocy 0,75 kW. Posiada on otwory rewizyjne, co pozwala na łatwą kontrolę stanu kubełków i pasa.
Separator bębnowy, typu dynamiczno-podmuchowego SUSB1/1, oddziela duże zanieczyszczenia i pyły od ścierniwa nominalnego. Stopień i dokładność separacji reguluje się strumieniem powietrza podmuchowego. Wtrącenia duże i podfrakcja ścierniwa są wydalane automatycznie do pojemnika odpadowego. Pyły razem z powietrzem podmuchowym trafiają do dwukomorowego modułu filtracyjnego, natomiast ścierniwo nominalne opada do zbiorników zasobowych. Separator jest wyposażony w napęd bębna o mocy 0.25 kW .
Pod separatorem magnetycznym zainstalowano zbiornik zasobowy SUZBZ0,6/1 o pojemności 0,6m3. Umieszczony nad dozownikiem, dostosowany do automatycznego zasypywania dozownika ścierniwa.
Pod zbiornikiem zainstalowano jednostanowiskowy dozownik ścierniwa, o poj. 200 dm3 SU DZ 1/200 SP z automatyką pneumatyczną, posiadający:
- zawór dozujący do śrutu,
- moduł sterowania pneumatycznego RMS 2000,
- dźwignia RLX-III,
- dopuszczalne ciśnienie robocze – 1MPa.
- reduktor do regulacji ciśnienia,
- parametry węzą i dyszy zostaną wybrane przez Inwestora (np. wąż o długości 10m zakończony dyszą)
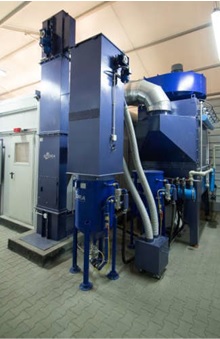
Instalacja sterująca i elektryczna
Komora jest wyposażona w zintegrowany moduł sterująco-zasilający SUMSZ10/2. Moduł jest oparty na systemie mikroprocesorowym, sterującym pracą wszystkich urządzeń zainstalowanych w śrutowni. Zawiera układy sterujące kolejnością włączania i wyłączania poszczególnych urządzeń, układem blokad i zabezpieczeń oraz sygnalizacją stanów awaryjnych.
Zastosowane sterowanie pozwola na sprzężenie dozownika z wyłącznikami krańcowymi dla bram oraz drzwi obsługowych, lamp sygnalizacyjnych i układem dźwiękowym.
W komorze zainstalowano urządzenia o następującej mocy:
- oświetlenie 0,6 kW
- moduł filtrujący SUMF10/2 11 kW
- separator ścierniwa SUSB1/1 0,25 kW
- podnośnik kubełkowy SUPK100/5 0,75 kW
- podłoga zgarniająca SUPZ5.3/E ok. 3,6 kW
Urządzenia zasilane napięciem:
- napięcie zasilania 3 x 400/230 (TN-C-S),
- napięcie sterowania 220 V, 50 Hz, 12 i 24 V DC
- napięcie lampek kontrolnych 24 V DC,
Komora posiadała układy wzajemnych blokad i sygnalizacji zapewniające bezpieczną pracę :
- sygnalizator świetlny pracy komory,
- automatyczne wyłączanie trybu pracy po otwarciu bramy lub drzwi,
- blokada pracy przy otwartej bramie lub drzwiach,
- automatyczne wyłączanie oczyszczarki przy upuszczeniu węża przez operatora,
- włączanie i wyłączanie oczyszczarki przez operatora
- przycisk bezpieczeństwa w komorze
- sygnał dźwiękowy bezpieczeństwa.
Kolejność włączania i podział poszczególnych odbiorników będzie następująca:
- wentylacja nawiewno-wyciągowa,
- oświetlenie,
- system recyrkulacji ścierniwa,
- podłoga zbierająca
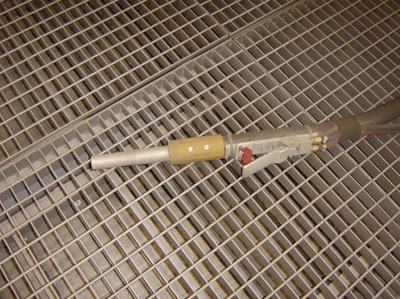